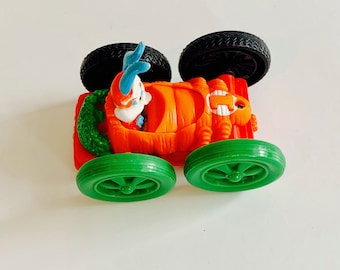
Material Selection: The most common materials used in diecasting for toy vehicles are zinc and aluminum alloys due to their durability and malleability.
Mold Preheating: Molds are preheated to ensure the molten metal flows smoothly and to reduce thermal shock, which can damage the mold.
2. Melting the Metal
Furnace Melting: The selected metal alloy is melted in a furnace at temperatures typically ranging from 700�C to 800�C (1292�F to 1472�F) for zinc alloys, and slightly higher for aluminum.
Maintaining Purity: Impurities are skimmed off the surface of the molten metal to ensure a high-quality cast.
3. Diecasting Process
Injection: The molten metal is injected into the preheated mold under high pressure, typically between 1,500 to 25,000 psi (10 to 170 MPa). This pressure ensures the metal fills all the intricate details of the mold.
Fast Cycle Time: Diecasting is a fast process, with each cycle taking from a few seconds to a couple of minutes, depending on the part's size and complexity.
4. Cooling and Solidification
Controlled Cooling: After the mold is filled, the metal is allowed to cool and solidify. The cooling time varies but is carefully controlled to prevent defects.
Mold Opening: Once the metal has solidified, the mold is opened, and the cast part is ejected. The design of the mold includes ejection mechanisms to assist in the removal of the part.
5. Trimming and Cleaning
Removing Flash: Excess material, known as flash, forms around the part where the mold halves meet. This is trimmed off using specialized tools.
Surface Cleaning: The cast part is cleaned to remove any residues, oxides, or burrs resulting from the casting process. This can be done through mechanical or chemical means.
6. Finishing Processes
Surface Finishing: Parts may undergo additional finishing processes such as polishing, painting, or coating to enhance their appearance and durability.
Detailing: Decals, stickers, or additional components (like windows, tires, or interiors) are added to the cast part to complete the toy vehicle.
7. Quality Control
Dimensional Inspection: Each part is measured and inspected to ensure it meets design specifications and tolerances.
Defect Detection: Parts are checked for common casting defects such as porosity, cold shuts, or misruns. Non-destructive testing methods like X-rays or dye penetrant inspections may be used.
Functional Testing: Functional tests ensure that movable parts, such as wheels or doors, operate correctly.
8. Batch Production
High-Volume Casting: Diecasting allows for high-volume production runs, making it cost-effective for large quantities. A single mold can produce thousands of parts before needing maintenance or replacement.
Consistency: The process ensures that each cast part is nearly identical, maintaining consistent quality across the entire production batch.
9. Recycling and Waste Management
Recycling Scrap: Excess metal from trimming and defective parts are collected and recycled, reducing material waste.
Efficient Use of Resources: Modern diecasting processes are designed to minimize waste and optimize material use, contributing to more sustainable manufacturing practices.
10. Innovations in Casting
Advanced Alloys: New metal alloys are being developed to improve the strength, durability, and casting characteristics of toy vehicles.
Automated Systems: Increasing automation in the diecasting process enhances efficiency, precision, and reduces labor costs.
Smart Manufacturing: Integration of IoT and AI technologies for real-time monitoring and optimization of the casting process.
The casting process is pivotal in the production of diecast toy vehicles, ensuring high-quality, detailed, and durable products that appeal to both collectors and children.