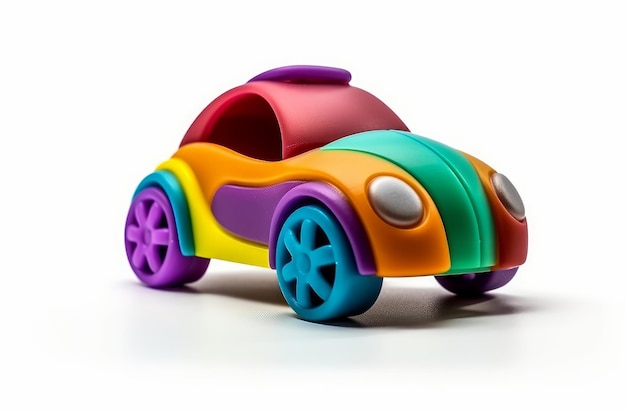
Detailed Blueprint: Based on the final design and prototype, detailed blueprints for the molds are created. This includes precise measurements and specifications for each part.
Material Selection: High-grade steel is typically used for molds due to its durability and ability to withstand the high pressures of the diecasting process.
2. Mold Fabrication
CNC Machining: Computer Numerical Control (CNC) machines are used to carve the molds from steel blocks. This process involves precise cutting and shaping to match the design specifications.
Electro-Discharge Machining (EDM): For intricate details and complex shapes, EDM is used. This process uses electrical discharges to erode material and create detailed patterns in the mold.
3. Mold Assembly
Multi-Part Molds: Molds are often made in multiple parts to allow for complex shapes and easy removal of the cast parts. These parts are assembled and aligned with high precision.
Alignment and Calibration: The assembled mold parts are calibrated to ensure they fit together perfectly and create a seamless cast.
4. Diecasting Process
Molten Metal Injection: Molten metal, typically a zinc or aluminum alloy, is injected into the mold under high pressure. This ensures that the metal fills all the intricate details of the mold.
Cooling and Solidification: Once the mold is filled, the metal is allowed to cool and solidify. Cooling times vary depending on the size and complexity of the part.
5. Mold Ejection
Part Removal: After the metal has solidified, the mold is opened, and the cast part is ejected. Ejection pins or mechanisms are often used to release the part without damaging it.
Trimming and Cleaning: Excess material, known as flash, is trimmed off. The cast part is then cleaned to remove any residues from the molding process.
6. Quality Control
Inspection: Each molded part undergoes a thorough inspection to check for defects, such as incomplete fills, surface imperfections, or misalignments.
Testing: Functional tests may be conducted to ensure the parts meet all specifications and performance standards.
7. Mold Maintenance
Regular Cleaning: Molds require regular cleaning to remove any residues or buildup that could affect the quality of future casts.
Repair and Maintenance: Molds are periodically inspected for wear and damage. Repairs are made as needed to maintain the precision and quality of the casts.
8. Mass Production
High Volume Casting: Once the molds are perfected and quality approved, they are used for high-volume production. The durability of steel molds allows for thousands of casts before needing replacement.
Consistent Quality: The precision and repeatability of the diecasting process ensure that each part is consistent in quality and detail.
9. Innovations in Molding
Advanced Materials: New alloys and materials are continually being developed to improve the strength, detail, and efficiency of diecast parts.
3D Printing of Molds: Advances in 3D printing technology allow for rapid prototyping and even direct printing of molds, reducing lead times and costs.
The molding process is a critical step in the production of diecasts and toy vehicles, ensuring that each piece is made with precision and consistency. This allows for the high-quality, detailed models that collectors and enthusiasts value.