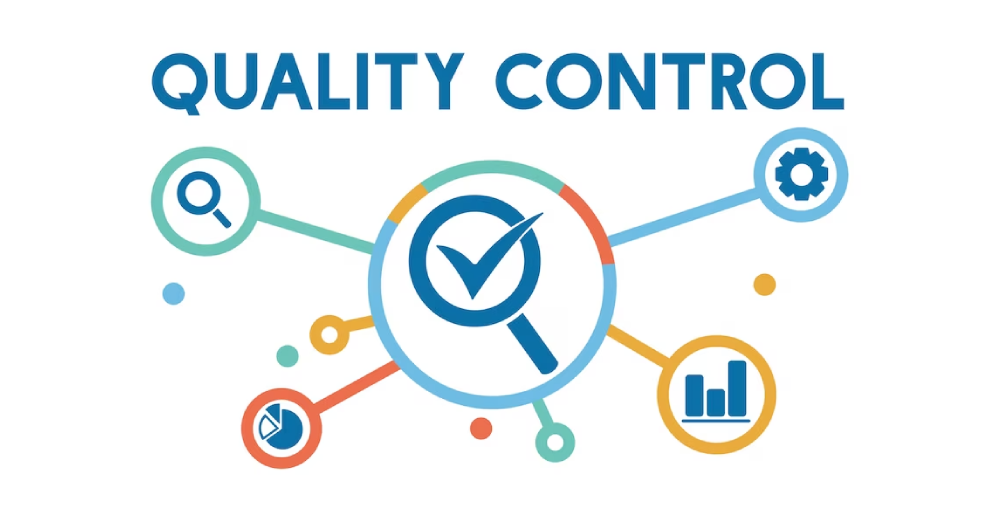
1. Inspection
Visual Inspection
Visual inspection is the first line of defense in quality control. Trained inspectors visually examine parts for obvious defects such as cracks, deformations, or surface imperfections. This step is crucial for identifying issues early in the process.
Dimensional Inspection
Dimensional inspection ensures that parts conform to specified measurements and tolerances. Tools such as calipers, micrometers, and coordinate measuring machines (CMM) are used to check the dimensions of the parts. This step ensures that parts will fit and function correctly in the final assembly.
2. Non-Destructive Testing (NDT)
Non-destructive testing methods are used to detect internal and surface defects without damaging the part. Common NDT techniques include:
Ultrasonic Testing
Ultrasonic testing uses high-frequency sound waves to detect internal flaws. This method is particularly useful for inspecting welds, castings, and forged parts.
Magnetic Particle Testing
Magnetic particle testing involves applying a magnetic field to the part and then sprinkling it with iron particles. Defects on or near the surface will cause the particles to gather, making them visible under ultraviolet light.
Dye Penetrant Testing
Dye penetrant testing involves applying a liquid dye to the surface of the part. After a set period, the dye is removed, and a developer is applied. The developer draws out the dye from any cracks or defects, making them visible.
Radiographic Testing
Radiographic testing, or X-ray inspection, is used to detect internal defects in castings and welded joints. It provides a detailed image of the internal structure of the part.
3. Functional Testing
Functional testing simulates real-world operating conditions to ensure that parts perform as expected. This step involves:
Load Testing
Load testing applies mechanical loads to the part to ensure it can withstand the forces it will encounter in service. This is particularly important for components such as suspension parts and engine mounts.
Thermal Testing
Thermal testing subjects parts to extreme temperatures to ensure they can operate effectively in varying conditions. This is essential for engine components and parts exposed to high heat.
Vibration Testing
Vibration testing simulates the vibrations that parts will experience during operation. This test is crucial for ensuring the durability of parts such as engine mounts, exhaust systems, and electronic components.
4. Material Testing
Material testing verifies that the raw materials used in the manufacturing process meet specified standards. Common material tests include:
Hardness Testing
Hardness testing measures the resistance of a material to deformation. It is used to ensure that parts have the necessary strength and wear resistance.
Tensile Testing
Tensile testing measures the tensile strength, yield strength, and elongation of materials. This test ensures that materials can withstand the forces they will encounter in service.
Chemical Analysis
Chemical analysis verifies the composition of materials to ensure they meet specifications. Techniques such as spectroscopy and chromatography are used to identify and quantify the elements in a material.
5. Process Control
Process control involves monitoring and controlling the manufacturing process to prevent defects from occurring. Key aspects of process control include:
Statistical Process Control (SPC)
SPC uses statistical methods to monitor and control the manufacturing process. Control charts and other tools are used to detect variations and trends that could indicate potential problems.
Process Audits
Process audits involve regular inspections of the manufacturing process to ensure compliance with standards and procedures. Audits help identify areas for improvement and ensure that corrective actions are implemented.
6. Certification and Compliance
Auto replacement parts must comply with industry standards and regulations. Certification ensures that parts meet these requirements. Common certifications include:
ISO Certification
ISO certification, such as ISO 9001, ensures that a manufacturer has a quality management system in place that meets international standards.
OEM Certification
OEM certification ensures that parts meet the specifications and requirements of the original equipment manufacturer. This is particularly important for aftermarket parts.
7. Final Inspection and Packaging
Before parts are shipped to customers, a final inspection is conducted to ensure they meet all specifications and quality standards. This includes:
Visual and Dimensional Inspection
A final visual and dimensional inspection is performed to ensure there are no defects or deviations from specifications.
Packaging Inspection
Parts are inspected to ensure they are packaged correctly to prevent damage during transit. Labels and documentation are checked for accuracy.
Conclusion
Quality control is an essential part of the manufacturing process for auto replacement parts. By implementing rigorous inspection, testing, and process control measures, manufacturers can ensure that their products meet the highest standards of quality and reliability. This not only enhances customer satisfaction but also contributes to the safety and performance of vehicles.